Lean Manufacturing
Advanced plastic cans, jars, bottles and other containers production with OUTSTANDING quality in every detail.
- Home
- Lean Manufacturing
Lean Manufacturing Since 2008
At Outstanding, lean manufacturing is at the heart of everything we do, benefiting both us and our customers. By optimizing processes, we minimize waste, lower costs, and reduce environmental impact, all while delivering high-quality, sustainable packaging solutions for your business.
Benefits for Our Clients
-
Direct Cost Savings
-
Ultra-Fast Market Response
-
Product Quality Assurance
-
Elimination of Supply Chain Risks
How Do We Achieve Lean Manufacturing?
OUTSTANDING's Numbers Speak for Themselves
3-5 Days
Fast Delivery Time
Rapid Sample Production
0
Hours
Extremely Low Defect Rate
0
%
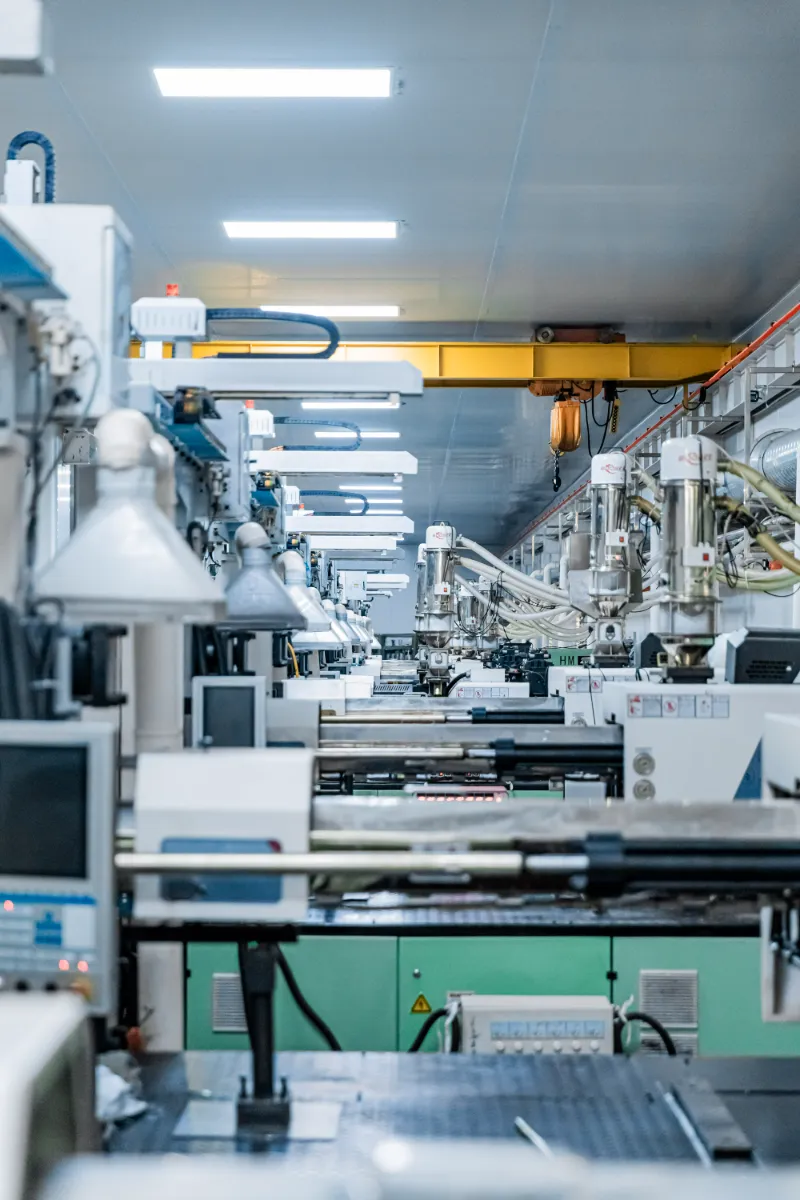
Customer Return Rate
<
0
%
High Production Efficiency
0
Million Units Daily
High Customer Satisfaction
0
%
A Detailed Look at Plastic Packaging Manufacturing
Raw Material Preparation
We use plastic materials that meet product requirements, such as PET. PET is first dried to remove moisture and improve molding quality, with specific temperature and humidity controls:
- Drying Temperature: 140-180°C (recommended 160-175°C)
- Drying Time: 4-6 hours (depending on moisture content)
- Dew Point: ≤ -40°C
- Moisture Content: ≤0.005% (50ppm)
- Hot Air Flow: 1.85 m³/kg·hr (ensuring thorough drying)
Injection Molding (Preform Production)
- Heating and Plasticization: PET pellets are melted to a molten state.
- Injection Filling: Molten plastic is injected into preform molds, with weight controlled to ±1.2g, and cycle time adjusted based on weight and temperature.
- Cooling and Shaping: The preform cools and solidifies in the mold.
- Preform Extraction: A robotic arm removes the preform for inspection.
Preform Storage or Preheating
Based on the production schedule:
- Preforms can be sent directly to the blow molding process or stored for later use.
- If stored, they need to be reheated to soften before blow molding.
Blow Molding
- Heating the Preform:The preform is heated to the required temperature in an infrared zone.
- Stretch Blow Molding: The preform is stretched vertically with a rod, then inflated with high-pressure air to shape it to the mold.
- Cooling and Shaping: After cooling, the container is removed from the mold.
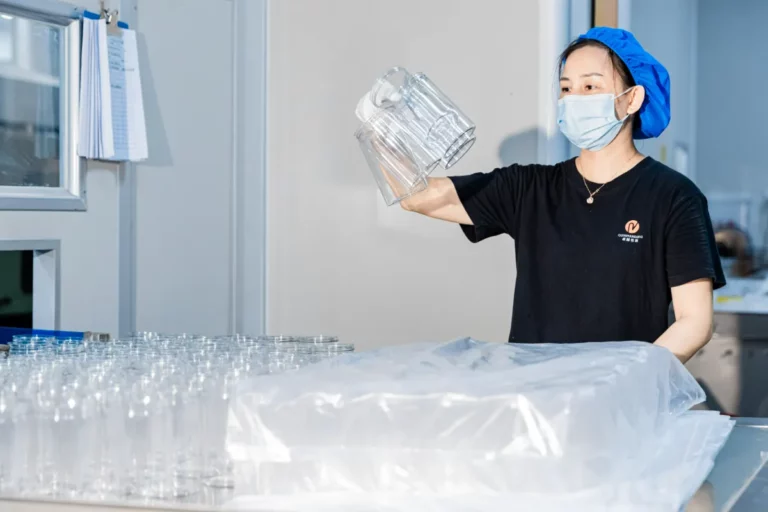
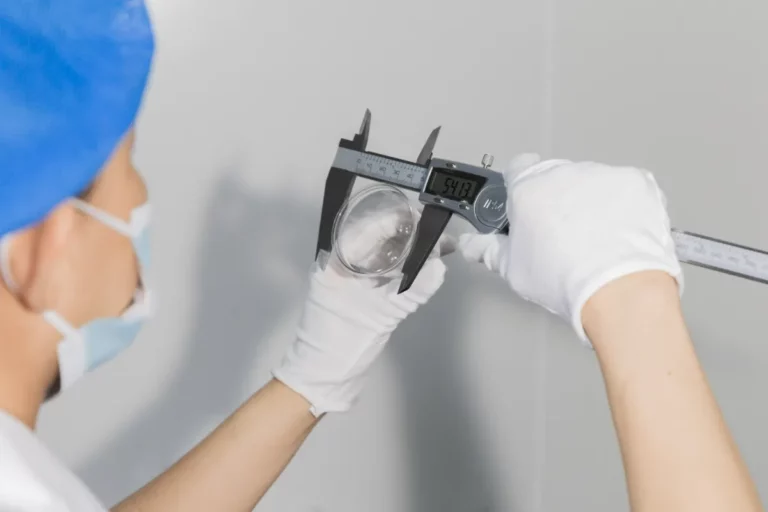
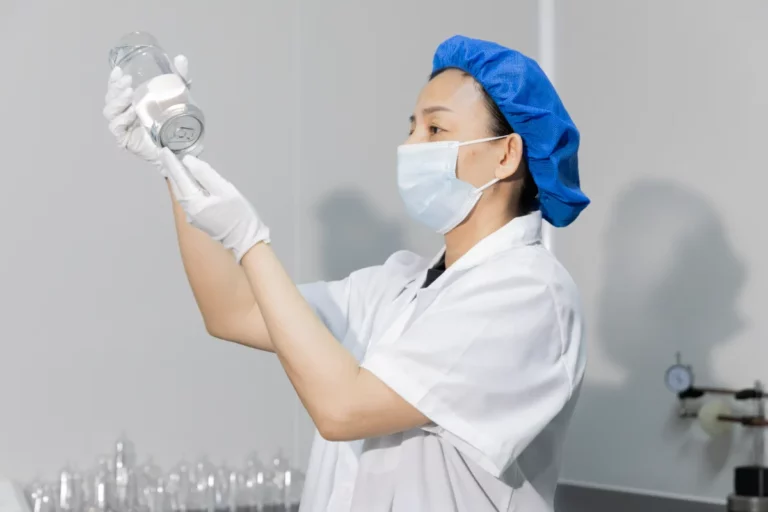
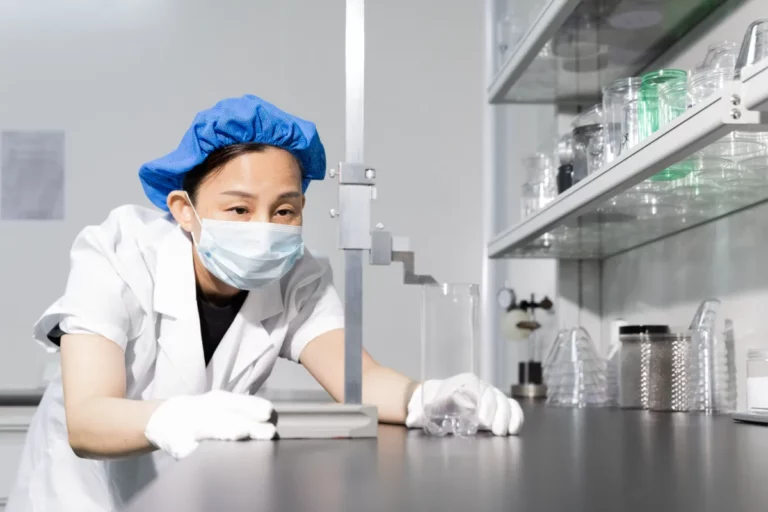
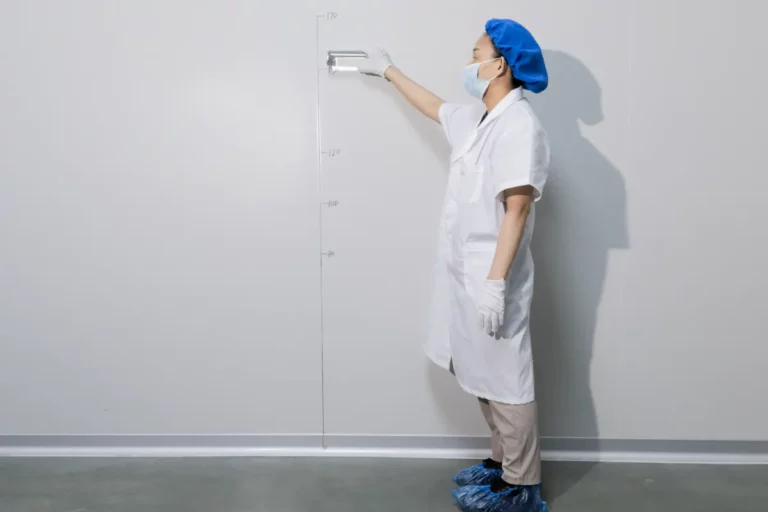
Quality Check
We guarantee a 99.8% yield rate to ensure the final product meets customer specifications.
- 100% Appearance Inspection
- Dimensional Measurement
- Sealing Test
- Compression Strength Test
- Drop Test
Printing and Labeling
We offer options like silk-screen printing and labeling based on your needs, ensuring your branding is clear and securely applied.
Packaging and Storage
We package according to customer preferences, offering options like reinforced cartons, stretch film, shrink bags, and pallets. Batch labels are applied before storing the products, ready for shipment.
Ready to Start Production of Your Bottles?
Get Your Custom Quote in 24 Hours
- Free samples available
- Low MOQ for trial orders
- Professional technical consultation